Better Deal Machinery is a highly valued branded company for manufacturing and supplying nitrogen plant and nitrogen generator and equipment. The company is situated at sprawling factory in Delhi NCR region and has one of the largest air separation testing centers where working of the plants is simulated before they are cleared for shipment to the customers. We are the only company equipped with this facility which helps us in delivering high quality plant machinery. Since the establishment of the company in 1995, we have sold over 350 oxygen nitrogen to customers all over the globe.
Our designing of nitrogen gas plant streamlines and increases the efficiency. The company has created a niche for itself by supplying high quality products. Being a quality conscious business, we always endeavor to deliver products that are durable, efficient and low maintenance. In comparison with other companies, our prices are the most competitive and quality is at par with the best air separation plant manufacturing majors. We have captures significant share of the industrial gas market for nitrogen such food packaging, manufacturing of ammonia, metallurgy, inerting, etc.
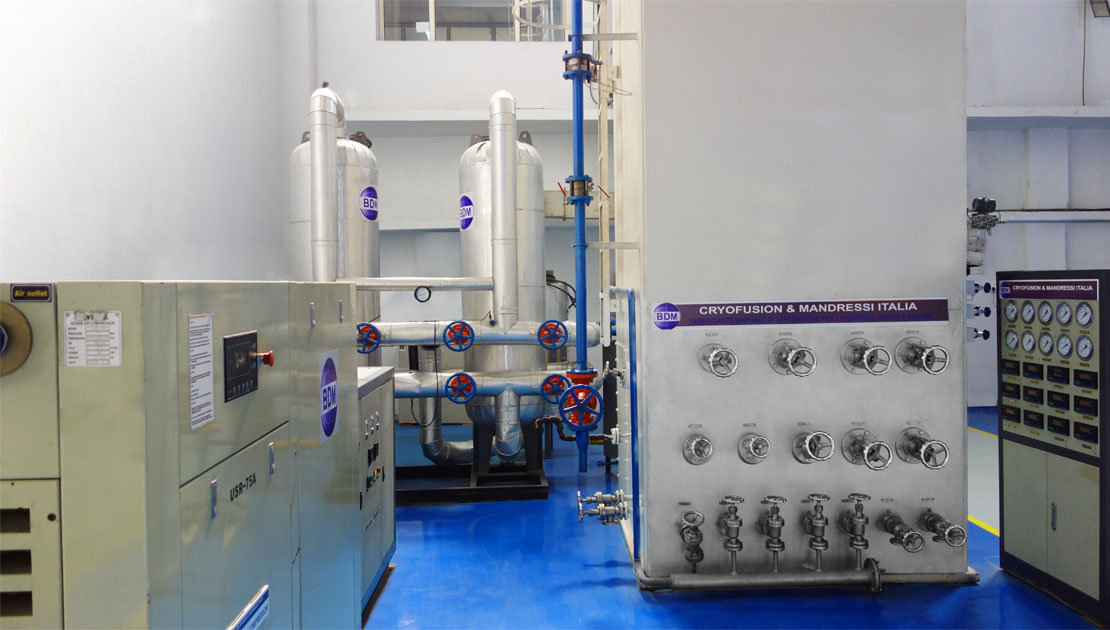
Manufacturing of the plant machinery is carried out in compliance with internationally accepted standards and practices. Only the high quality materials are used in the making of the machinery. BDM air separation column is made with cryogenic grade stainless steel. High precision TIG argon welding is used in the fabrication. Reputed brand as we are, it goes without saying that quality of our products is very important for us. The company has instituted strict quality control mechanism to ensure maintenance of the quality of the products as per standards mandated. Our nitrogen plant and other air separation products are certified by CE standards.
Salient Features :
- Internationally accepted standards of manufacturing
- Low capital requirement
- World-class designing
- Easy to install and operate
- Single operator can run the plant
- High grade stainless steel used in the fabrication of air separation column
- Leak-proof oil-free rotary type air compressors from Atlas Copco
- High purity nitrogen
- Cutting-edge cryogenic distillation technology
Technical Specifications
Capacity range : 20m3/hr to 1000m3/hr
Purity : Generates nitrogen with purity up to 99.99%
Type of welding : TIG argon welding
Electrical : NEMA standards
Basic Principle :
Nitrogen is generated through cryogenic process based on Linde process. It is starts by taking the air from the atmosphere which is subsequently filtered and compressed in the air compressor. Then the air goes into a purification unit where it is cleaned of all impurities. Next, the process air is passed through a series of heat exchangers where it is cooled to sub-zero temperatures to achieve liquefaction. From here the air is directed into a high pressure distillation column where it is separated into constituent gases oxygen and nitrogen. Here, nitrogen is collected and moved into a low pressure distillation column where it is distilled to meet desired purity specifications.
Scope and Supply of Nitrogen Plants
Air Compressors : It is the most vital component of the nitrogen plant so must be of world-class standards. We use leak-proof screw type centrifugal air compressor from Atlas Copco, the most valued brand for the component.
Pre-Cooling System : Pre-cooling systems comes pre-mounted on the process skid which is pre-piped and pre-tested. It is set to keep the temperature around 12 degrees Celsius of the all the equipment including the purification system.
Purification Unit : BDM uses high quality WIKA German purification unit which have ZEOCHEM molecular sieves known for their high level of performance. Swiss Zeolites are known for their efficiency. There is no recurring cost of chemicals.
Cryogenic Cooling of Air by Turbo Expander : The process air needs to be cooled to cryogenic temperatures to achieve liquefaction. Turbo expanders are used of providing cooling and cryogenic refrigeration for cooling the air to temperatures to sub-zero levels-165deg C to -170 deg C.
Separation of Liquid Air into Oxygen Nitrogen by Air Separation Column : After being purified in the purification unit, the air moves into a low pressure fin type heat exchanger where the air is cooled to cryogenic temperatures by air expansion process in the turbo expander. Thermal efficiency of the column being very efficient, it is crucial in assisting in achieving a temperature difference delta T around 2 degrees Celsius at the warm end of exchangers. The process gets separated into oxygen and nitrogen on entering air separation unit by the process of rectification. Oxygen is obtained at the outlet with purity of 99.7%. And, nitrogen we get at the outlet with purity up to 99.99%.
Compression of Oxygen Filling in the Cylinder : The final product is got by the liquid nitrogen pump that vaporizes liquid nitrogen at a high pressure of 150 bar or higher as may be required for cylinder filling or delivering into a pipe line supply or for captive consumption.
Industry Benefits
It is used to make nitric acid, nylon, fertilizers, explosives and dyes. Making of these products would require nitrogen to be reacted with hydrogen to produce ammonia.
Nitrogen is needed for making of amino acids, proteins, nucleic acids, etc. Plants absorb nitrogen through the roots in the form of ammonia or nitrate.
Nitrogen is a very important gas for the chemical industry. It is used to make fertilizers, nitric acid, dyes and nylon. The gas is colorless, odorless and tasteless.
Nitrogen is colorless, odorless and non-flammable gas known for its inert properties which displaces oxygen. So the main hazard associated with the gas is asphyxiation.